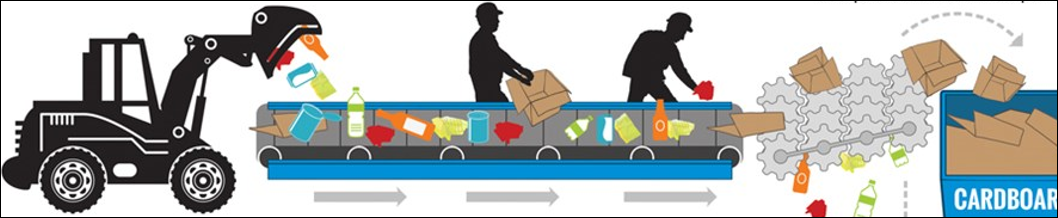
Published: 2024-03-19 Author: Ken Edwards
Single stream blue box recycling plays a critical part in reducing London Health Sciences Centre’s (LHSC) environmental footprint. But have you ever wondered what happens to your recyclables after they are collected? One essential part of the recycling process occurs at Material Recovery Facilities (MRFs), where these materials are sorted, processed, and prepared for reintegration into the production cycle.
The Role of Material Recovery Facilities
Material Recovery Facilities are large-scale recycling centres where mixed recyclables are separated, cleaned, and processed for further use. MRFs are the bridge between curbside collection and the industries that will convert these materials into new products.
Although arrangements vary across the country, in London, the city owns a facility that is operated by Miller Waste. Regulatory compliance of these facilities is overseen by the Resource Productivity and Regulatory Authority (RPRA) under the Ministry of Environment, Conservation and Parks.
Collection and Delivery
Recyclables collected from homes and businesses are transported to MRFs directly or through an intermediate transfer station. At this stage, materials can sometimes be lightly contaminated due to mistakes in mixing non-recyclables with recyclables by the initial people recycling or even at the transfer station.

Initial Sorting
Once the materials arrive at the MRF, the first step is to separate them into broad categories. Conveyor belts, rollers, and other equipment are used to move the recyclables along, while manual labour is also involved. Common categories include paper, cardboard, plastic, glass, and metal.
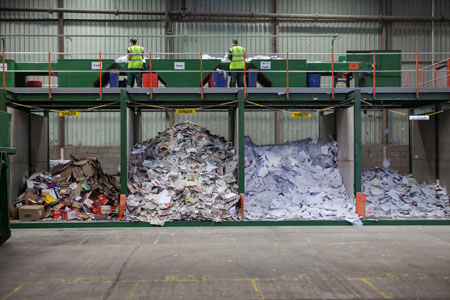
Automated Sorting
MRFs utilize various technologies, such as optical sorters, magnets, eddy current separators, and air classifiers, for the efficient sorting of materials. Optical sorters, for instance, can identify and separate different types of plastics based on their polymer composition. Magnets are effective for removing ferrous metals like steel cans, while eddy current separators can separate non-ferrous metals like aluminum.
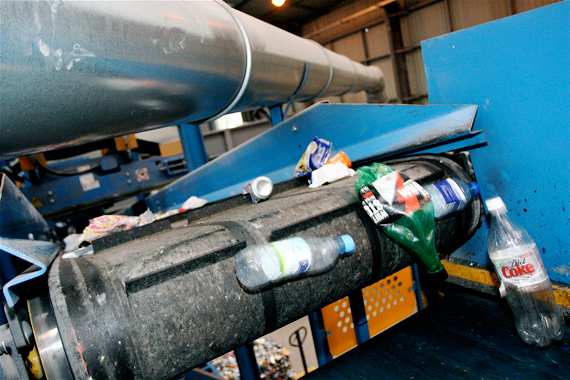
Baling and Shipping
Once the materials have been sorted and contaminants removed, they are compacted into bales or bundles for transportation to manufacturing facilities. Bales make the shipping process more efficient and cost-effective. For instance, cardboard and paper are commonly baled together, while plastics, metals, and glass are processed separately.
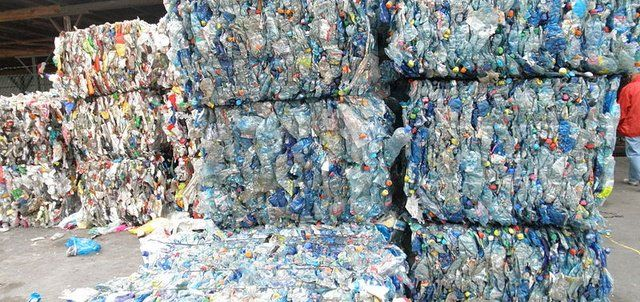
Quality Control and Contamination Management
The goal at MRFs is to recover as much recyclable material as possible. However, some contamination is inevitable when items are placed in the wrong bin or the wrong compactor. Contaminants like food waste, non-recyclable plastics, and other non-recyclables (e.g. masks, gloves, disposable gowns) must be removed.
While MRFs have quality control processes in place, including manual inspection, air blowers, and screening technologies to minimize contamination levels, these facilities are simply not equipped to handle high volumes of these waste materials. As shown in the pictures below, non-recyclables in the recycling stream can pose a safety hazard to MRF line workers and can cause damage to sorting equipment.
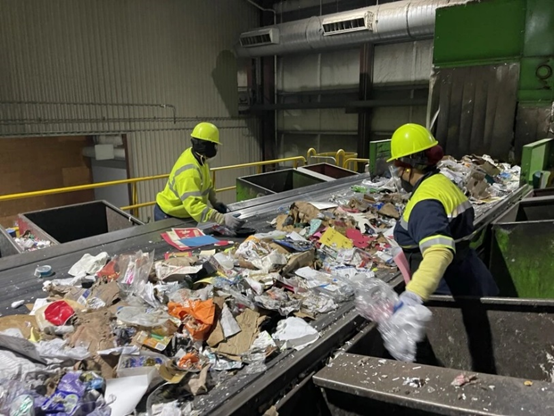
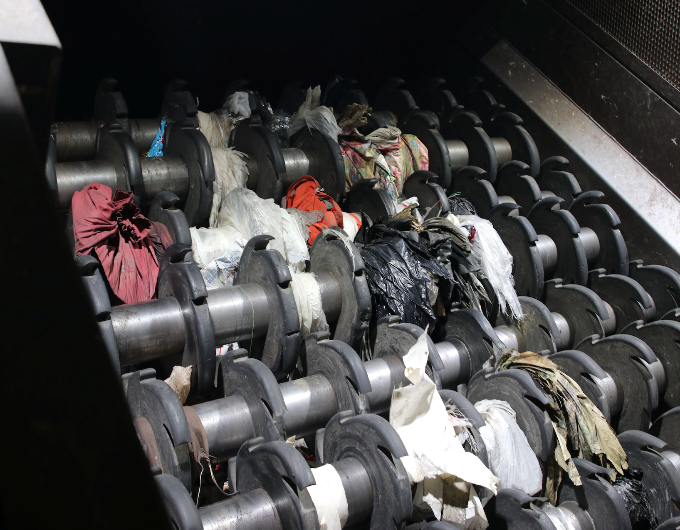
Conclusion
Material Recovery Facilities and their workers are critical to recycling. They play a vital role in transforming our recyclables into valuable resources for new products. Even when recycling is lightly contaminated, MRFs have the technology and expertise to ensure that these materials can still be recycled effectively. Along with ever improving technology, evolving methods, and new initiatives to improve efficiencies in the recycling industry, it is essential for all of us to do our part by understanding what can and can’t be recycled and by recycling responsibly to support ongoing recycling efforts. By working together, we can continue to reduce waste, conserve resources, and protect our environment for future generations.